|
|
|
|
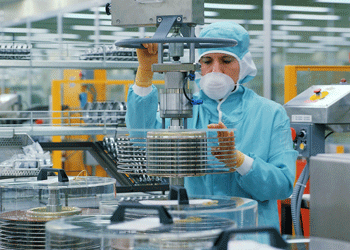 |
 |
Ask for our complete package of features and service solutions
in Lean.
We provide pre-studies and you get a second opinion how to
improve the efficiency and quality.
It takes from 3 days up to 4 weeks.
Prologia offers LEAN
approach for your processes. Now you can
optimize your work stream by using our Lean
expertise and methods in
- Waste time elimination
- Reduce Over-production or service
- Eliminate Waiting-time
- Eliminate material flow that doesn’t support
immediate production
- Keep only value adding processing
- Inventory reduction with JIT philosophy
- Motions study and balancing to eliminate waste
- Defects reduction and eliminate rework and repair
- Value Stream mapping
- Is a Lean technique used to analyze the flow of materials
and information currently required to bring a product or service
to a consumer. At Toyota where the technique originated, it is
known as "Material and Information Flow Mapping".
- Value stream mapping is a helpful method that can be
used in Lean environments to identify opportunities for
improvement in lead time. Although value stream mapping is
often associated with manufacturing, it is also used in
logistics, supply chain, service related industries,
healthcare[3], software development, and product
development.
We can identify seven
value stream mapping tools and they are:
1 Process Activity
Mapping
2 Supply chain
responsiveness matrix
3 Product Variety
Funnel
4 Quality filter
mapping
5 Forrester effect
mapping
6 Decision point
analysis
7 Overall Structure
Maps
- KanBan systems in sourcing from suppliers
-
Kanban maintains inventory levels -
a signal is sent to produce and
deliver a new shipment as material
is consumed. These signals are
tracked through the replenishment
cycle and bring extraordinary
visibility to suppliers and buyers
- KanBan systems internally
- Kanban is a signaling system to trigger action. As its name
suggests, kanban historically uses cards to signal the need for
an item. However, other devices such as plastic markers (kanban
squares) or balls (often golf balls) or an empty part-transport
trolley or floor location can also be used to trigger the
movement, production, or supply of a unit in a factory.
- 5 S implementation
- 5S is a reference to a list of five Japanese words
which 'start' with S. This list is a mnemonic for a methodology
that is often incorrectly characterized as "standardized
cleanup", however it is much more than cleanup. 5S is a
philosophy and a way of organizing and managing the workspace
and work flow with the intent to improve efficiency by
eliminating waste improving flow and reducing process
unreasonableness.
- Continuous Improvement solutions using Kaizen
-
In the context of this article, Kaizen refers to
a workplace 'quality' strategy and is often
associated with the Toyota Production System and
related to various quality-control systems.
Kaizen aims to eliminate waste (as defined by
Joshua Isaac Walters "activities that add cost
but do not add value"). It is often the case
that this means "to take it apart and put back
together in a better way." This is then followed
by standardization of this 'better way' with
others, through standardized work.
- TPM (Total Productive Management)
- TPM is a new way of looking at maintenance, or
conversely, a reversion to old ways but on a mass scale. In TPM
the machine operator performs much, and sometimes all, of the
routine maintenance tasks themselves. This auto maintenance
ensures appropriate and effective efforts are expended since the
machine is wholly the domain of one person or team. TPM is a
critical adjunct to lean manufacturing. If machine uptime is not
predictable and if process capability is not sustained, the
process must keep extra stocks to buffer against this
uncertainty and flow through the process will be interrupted..
One way to think of TPM is "deterioration prevention" and
"maintenance reduction", not fixing machines.
- Visual management
- Makes problems visible and helps staff staying in direct
contact with the reality
- Set-up times reduction using SMED (Single Minute Exchange
of Dice) originally from Toyota
- Is one of the many lean production methods for reducing
waste in a manufacturing process. It provides a rapid and
efficient way of converting a manufacturing process from running
the current product to running the next product. This rapid
changeover is key to reducing production lot sizes and thereby
improving flow
- JIT solutions
- Is an inventory strategy implemented to improve the return
on investment of a business by reducing in-process inventory and
its associated costs.
- Cellular Manufacturing
- is a model for workplace design, and is an integral part of
lean manufacturing systems. The goal of lean manufacturing is
the aggressive minimization of waste, called
muda, to achieve maximum efficiency of resources. Cellular
manufacturing, sometimes called cellular or cell production,
arranges factory floor labor into semi-autonomous and
multi-skilled teams, or work cells, who manufacture complete
products or complex components. Properly trained and implemented
cells are more flexible and responsive than the traditional
mass-production line, and can manage processes, defects,
scheduling, equipment maintenance, and other manufacturing
issues more efficiently
- Takt time introduction
- Can be defined as the maximum time allowed to produce
a product in order to meet demand. It is derived from the German
word taktzeit which translates to clock cycle. There is a logic
therefore to setting the pace of production flow to this takt
time. Product flow is expected to fall within a pace that is
less than or equal to the takt time. In a lean manufacturing
environment, the pace time is set equal to the takt time.
|
|
|
|
|